Ensuring the quality of foam from its formulation to final application is of utmost importance to avoid drastic consequences in its use.
One example is the role of mattresses in people’s daily lives. A mattress plays an essential role in providing comfort, relaxation, and quality of life to its users. However, if the mattress is of dubious quality, it can lead to serious issues for the user, such as body aches, breathing problems, and more.
Therefore, it is extremely important to conduct foam quality tests to ensure compliance with all the requirements stipulated by the existing market standards.
The Fundamental Role of Standards and Tests
There are specific standards from regulatory bodies (both national and international) for each type of application, such as mattresses, pillows, and others, aiming to ensure that these foams achieve the best quality and performance in the final product.
Common Laboratory Tests for Flexible PU Foams
The most common laboratory tests applied to flexible PU foams include:
Determination of Tensile Strength and Elongation – ABNT NBR 8615
Tensile strength refers to the relationship between the force required to break the foam and the dimensions of the sample, expressed in kPa. Elongation measures the extension of the foam until its rupture, expressed as a percentage (%).
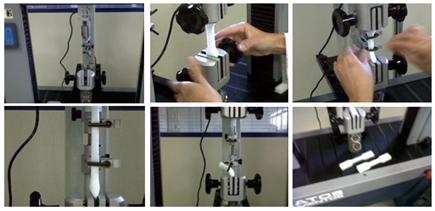
Determination of Compression Resistance – ABNT NBR 8910
This test measures the foam’s ability to withstand compression. It involves determining the force required to compress the foam to 50% of its thickness. Results are expressed in kPa.
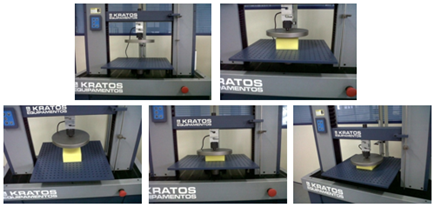
Determination of Permanent Compression Deformation – ABNT NBR 8797
This test measures the difference between the initial and final thicknesses of a foam sample after being subjected to specific compression under set temperature, humidity, and time conditions.
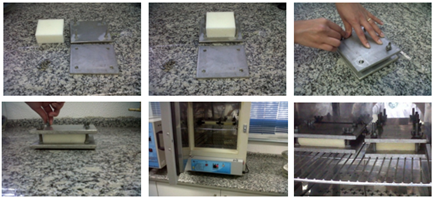
Determination of Apparent Density – ABNT NBR 8537
Density, expressed in Kg/m³, is the ratio of a material’s mass to its volume. This property must be controlled as variations can affect the foam’s physical characteristics, such as touch, resilience, permanent deformation, and support. Density also impacts foam yield and production efficiency.
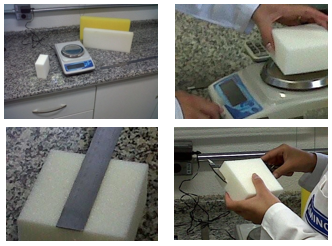
Determination of Dynamic Fatigue – ABNT NBR 9177
This test deflects the sample to 70% of its thickness using a standardized indentor for 80,000 cycles. Results are analyzed in terms of percentage losses in thickness and load-bearing capacity.
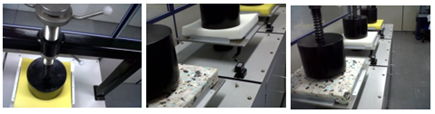
Determination of Combustion Characteristics – ABNT NBR 9178
This test involves applying a flame to the sample for a set time and then measuring the burn propagation in mm/min and the duration in seconds after the flame extinguishes.
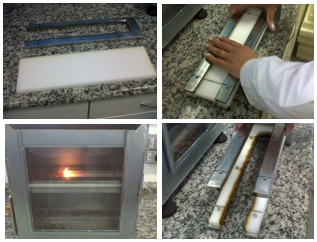
Determination of Indentation Force and Comfort Factor – ABNT NBR 9176
Indentation force is used to measure the foam’s load-bearing capacity, expressed in Newtons (N). This parameter ensures that the foam meets the specified hardness standard. Variations in hardness can indicate raw material inconsistencies or formulation errors.
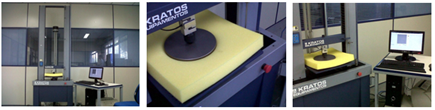
Determination of Tear Resistance – ABNT NBR 8616
This test measures the resistance of foam to tearing under tension, expressed in N/m. It evaluates the suitability of the foam for applications where shear and tensile forces are present.
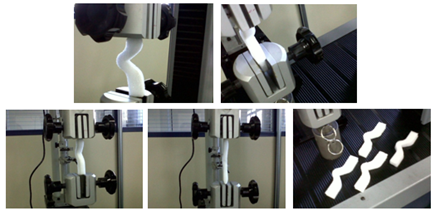
Discover the Article: “[Complete Guide] Everything You Need to Know About Flexible Foams” [Click Here]
Technology for Flexible Foams
Amino provides the most comprehensive range of solutions for Flexible Polyurethane Foams.
Our portfolio includes Silicones, Amines, Pigments, Additives, Binders, and ready-to-use systems. Additionally, our technical team comprises the best polyurethane specialists to assist and guide customers, combining high-quality raw materials with process efficiency.
Amino’s Solutions for Flexible Foams
- Performance Additives
- Silicone Surfactants
- Amine Catalysts for Expansion and Gelling
- Delayed Catalysts
- Low VOC Catalysts
- Tin Octoate
- Liquid and Paste Pigments
- Adhesion Promoters (flame bonding)
- Open Cell Additives
- Additives for Elongation and Tearing
- Hardness Additives
- Anti-Scorching Additives
- Halogenated and Non-Halogenated Flame Retardants
Ready-to-Use Flexible Systems
- Viscoelastic for MDI Block Process
- Viscoelastic for TDI Block Process
- Viscoelastic for Molded MDI Process
- Hyper Soft Systems for TDI Block Process
- Hyper Soft Systems for Molded MDI Process
- Flexible HR Systems for MDI and TDI Block Processes
- Flexible HR Molded Systems for MDI and TDI
- Complementary Products for Flexible Foams
- Rebonded Foam Glue
- Foam-to-Fiber Adhesive
- Gel Sheets
For more information about Amino Technology, contact us at +55 11 4077-3777 or email us at vendas@amino.com.br.
About Amino
Flexible PU foams play a fundamental role in various industries, and choosing the right system and additives is crucial to achieving the desired performance. If you want to learn more about how to optimize your production processes and explore Amino’s complete line of additives and solutions, contact us. We are ready to help you find the best solutions for your production needs!