Function of Filters
The air filter is a fundamental component in any combustion engine, as its primary function is to retain any dirt particles that might enter and hinder the engine’s operation. Additionally, the air filter also helps reduce the engine’s intake noise.
The oil filter, on the other hand, is essential for trapping impurities resulting from engine operation or inadequate sealing, purifying the oil and preserving its quality. As a result, it helps maintain the engine’s performance and efficiency.
Fuel filters (for gasoline, ethanol, and diesel) play an important role in retaining impurities that may be present in the fuel or the tank, preventing these particles from reaching the injector nozzle or the pump. This helps protect internal components and prevents performance loss.
Another notable filter is the cabin filter. This filter is responsible for preventing harmful particles from the outside air from entering the vehicle’s interior through the air conditioning system or air vents. It captures soot, bacteria, mites, and other impurities, improving the air quality inside the vehicle.
Early Filters
In the automotive industry, early filters were made of metal with felt (a fabric made from wool or animal hair) inside and required O-rings for sealing, which increased the product’s overall cost. Additionally, these filters allowed some abrasives to pass through the system.
Eco-Friendly Air and Oil Filters and the Choice of Polyurethane
For several years, the production of air filters for motor vehicles has relied on polyurethane as a structural material for the filtering medium.
PU material stands out for its excellent resistance to various factors, such as deformation, stretching, tearing, and high temperatures. The shift to polyurethane began in the 1980s and, according to experts, is here to stay.
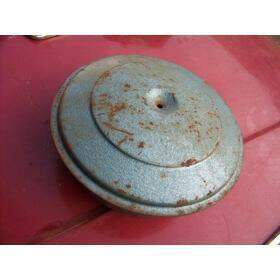
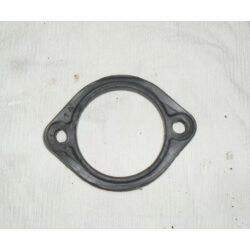
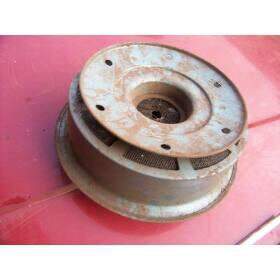
PU Filters Eliminate Old Sealing Rings and Are Much Better at Combating Dirt
In Eco-Friendly Oil Filters, Elastomeric Polyurethane provides better conditioning with high Shore A hardness, offering excellent resistance while ensuring the filter’s structure and sealing.
The Main Functions of Polyurethane in Filters Are:
- Material used as the base for the filter body
- Ensures a perfect fit of the filter in the engine’s air supply system
- Provides proper sealing so that all air passes through the filter rather than the mounting base
Key Advantages of PU in Filters
Polyurethane is one of the most efficient and versatile polymers available. In various types of filters, properly formulated PU ensures appropriate density, elongation, tear resistance, hardness, and permanent deformation, resulting in a higher-quality material and, consequently, superior performance for the end user.
In air filters, polyurethane combines high mechanical strength with low density, helping to reduce fuel consumption due to efficient filtration.
Additional advantages of using polyurethane in filters include:
- High retention capacity and extended service life of the part
- Eliminates the need for sealing filter edges: reduces manufacturing costs and operational risks during production
- Outstanding elongation, tear resistance, and deformation resistance
- Good resilience
- High temperature resistance
- High elasticity
- Flexibility
- Low hardness
Manufacturing Air Filters Structured with PU
The manufacturing process is simple, typically involving casting. Casting-based production consists of four steps:
- Prepare the filter mold in the shape of the filtering material (rectangular or circular).
- Apply PU, resulting from the mixture of the two main components (polyol and isocyanate), to the mold edges.
- While the foam expands at the mold edges, the filtering element is applied.
- Allow the PU to cure. Once cured, the filter is ready.
In this type of application, PU must have good fluidity to reduce production time and increase customer productivity.
Air filters structured with PU are typically produced using pre-formulated PU systems. Multinational companies often adopt this manufacturing method, as pre-formulated polyurethane systems allow customers to focus on filter production while improving convenience and productivity. The manufacturing process requires a stringent quality system, usually allowing a maximum of seven defects per million units.
The chemical base of the filter is usually polyether due to its excellent mechanical properties. The PU densities used depend on the client’s specifications.
The air filter mainly consists of pleated paper (similar to an accordion), and some include metal screens (internal and external) fixed with a high-resistance material like polyurethane. PU acts as a sealing element to ensure impure air does not bypass the filter and contaminate the engine. The filtering element is housed within the casing, and once the cover is placed, air only passes through this paper, which retains dust and other particles effectively.
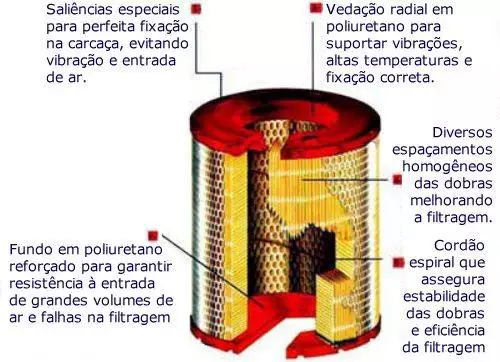
Material Quality and Cleanliness
When assembling the filter into the housing, it is typically required that the PU structure creates tension during installation to ensure a perfect fit with the filtering structure, preventing the passage of unwanted particles through the filter.
PU must provide excellent sealing of the air system to avoid damage to the engine assembly.
Other required properties include compression set resistance and dimensional stability (shrinkage resistance).
Do not use aggressive substances (e.g., solvents) when cleaning the filter. These aggressive substances can react with PU, leading to premature deterioration of the part.
Where to Find the Best Polyurethane Technology for Filters
It is crucial to find a company that not only offers a wide range of high-quality polyurethanes for use in filters but also provides technical support to help clients achieve the perfect product. For this reason, Amino has been a market reference for 35 years, delivering custom formulation solutions for every type of process, as well as high-quality raw materials.
Amino operates nationwide and also exports to several countries.
To learn more about Amino Technology, contact us at 4077-3777 or click here to send us an email: vendas@amino.com.br
About Amino
Flexible PU foams play a fundamental role in various industries, and choosing the right system and additives is crucial to achieving the desired performance. If you want to learn more about how to optimize your production processes and explore Amino’s complete line of additives and solutions, contact us. We are ready to help you find the best solutions for your production needs!